You can’t reinvent the wheel. Or can you? It’s been done successfully at least once: with containers. The worldwide consignment industry had a complete overhaul. Clothing, machinery, fruit, grains, toys and much more were all transported in an entirely new way – one that was standardised to set new benchmarks in the construction of ships, ports and trucks.
Because suddenly all transport problems were reduced to the dimensions of 20, 40 and 45 feet. Labyrinthine ship cargo holds, or indeed a capsizing risk resulting from sliding loads? Laboriously loading and unloading each individual item by loader crane and hand? Within the space of a few decades, this all became a thing of the past.
But as they so often do, some solutions bring their own set of problems. And when it comes to containers, this is the very load itself.
In cases involving heavy, bulky cargo, a worldwide standard is replaced by improvisation. While this is not inherently a bad thing, it is just time-consuming and dangerous: Staff lie prostrate on the container roof co-ordinating, or at least trying to co-ordinate, a forklift in front of the container and their colleagues below inside the container. It’s a common sight. But even old-hands are limited in what they can do if the cargo starts sliding during loading. Then all they can do is hope that no one is inside the container, and that the shipper is well insured. A carefully manufactured product getting damaged just before delivery is a nightmare for everyone involved.
Viewed objectively, however, this really does raise the question of how this daily practice can be compatible with omnipresent process optimisations in production or a company’s compliance regulations. Not to mention profitability.
SIMPLY. Container Loading System: One Stop Flexible Solution
Staff who spend hours loading a container cannot work productively.
Equipment used for hours to load a container cannot fulfil its duties elsewhere.
Open top containers are certainly one solution. Albeit an expensive one.
This was in turn the basis for developing container-loading systems. Most, however, require additional measures or have only been designed for special purposes.
One typical example are ramps which trucks need to line up against with millimetre-precision, or steel gates, often with elaborate scanning and sensor equipment. This is undoubtedly an advantage when loading and unloading standardised goods. These sorts of container-loading systems are often fully automated and integrated into a large warehousing system. But they’re just not suitable for non-standard goods like steel components, pipes or funicular pulleys. They only enable you to load. With SIMPLY., on the other hand, you can also unload containers which have been previously loaded with SIMPLY. Many SIMPLY. customers take advantage of this for their internal logistics projects.
Other container-loading equipment operates with a type of flexible platform, on which the cargo sits, and which is then violently dragged back down and out of the container once loading is complete. It’s one conceivable solution, but certainly not for high-quality or fragile goods.
In sum: These solutions are expensive and inflexible. They are virtually out of the question for heavy, bulky goods, and require a specific infrastructure. This is where the SIMPLY. container-loading system reveals its full design advantages: In principle, it needs an asphalted or paved yard, though any sealed surface will do if necessary. It also needs an operating current and compressed air, though this can be produced by an in-built compressor if desired. Nothing more to it!
And that’s only the beginning if we’re talking about container-loading under the motto of “Easy, safe and fast”.
Particularly given that the SIMPLY. container-loading system really starts showcasing its strengths when dealing with cargo that cannot be schematically charted or loaded.
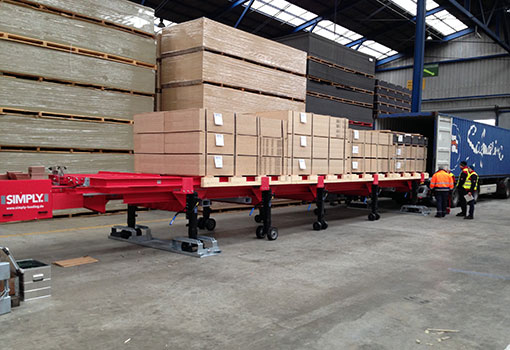
SIMPLY. Container Loading Solution: Time-saving and Cost-effective
The core idea is genius, and is also reflected in the name – SIMPLY.. The cargo sits on a pallet which is simply slid into the container.
This pallet is made from normal square timber, differing in length according to specific needs, and can be easily made on site. This itself provides an initial amount of freedom.
The next comes with the picking process, which is unique. Because the cargo can be pre-picked on the pallet. Without any of the stress that comes with a truck being in the yard and costing money; it’s instead completely hassle-free. The day before the truck arrives, a few hours prior – or just whenever it suits. All work is performed outside the container. In ideal lighting conditions and with lots of space. Staff no longer needs to go inside the actual container. You can’t get safer than that. And these perfect conditions also mean faster work.
Fragile or sharp-edged components can be carefully protected, and the cargo can be loaded without being damaged – sparing any irritation and warranty costs.
The loading process itself takes barely 10 minutes, and only requires one single staff member.
Their tasks are to wave in the truck, bring the SIMPLY. container-loading system in line with the truck’s sill (something any truck with a level adjustor can do), adjust the container length, check the power and compressed air are connected – and then press the button.
As such, the advantages can be summed up as follows: SIMPLY. directly saves you money by doing away with the need for open-top containers and shortening handling times. Forklifts and staff are more quickly available for productive work – and that also pays off. The cargo can be carefully protected and safely loaded, sparing you warranty and insurance costs. You also avoid having to worry about setting up costly infrastructure involving ramps and loader cranes. And SIMPLY. is insanely flexible when it comes to heavy, bulky goods; it has a load-bearing capacity of up to 30 tonnes. And the SIMPLY. container-loading system is suitable for all conventional sea containers.